RINGSPANN in Main & Boom Hoists and Trolleys
Electrohydraulic Thruster Brakes and Couplings for Hoists
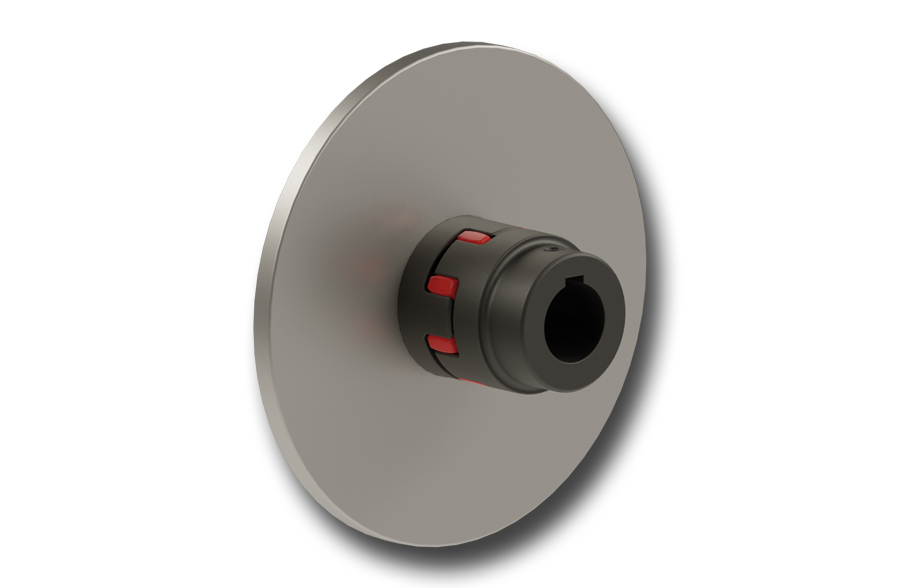
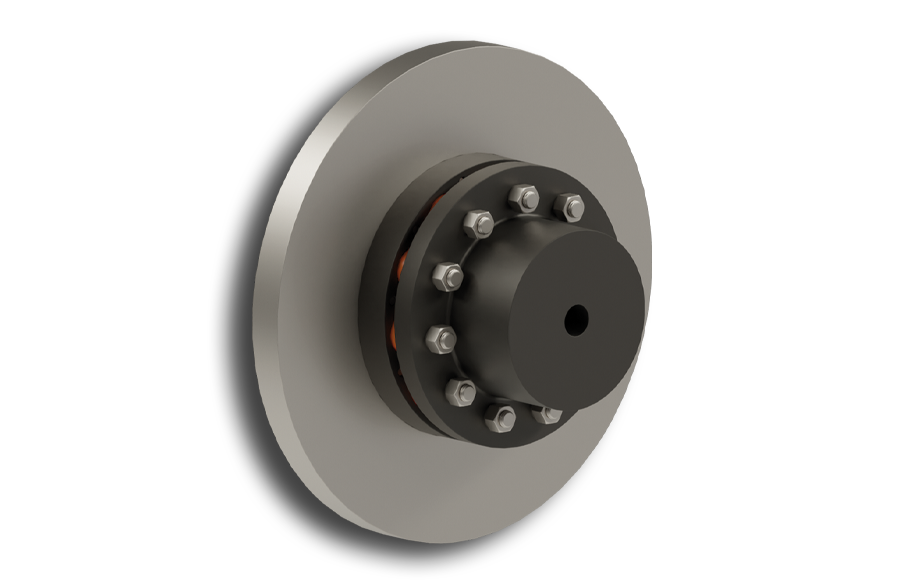
Pin and Bush and Jaw Couplings with Brake Disc
- Brake disc diameter up to 1 000 mm
- Maximum transmittable torques of up to 337 kNm
- Fail-safe torque transmission
- Compensation of axial, radial and angular misalignments
- Low maintenance
- Complies with ATEX 2014/34/EU
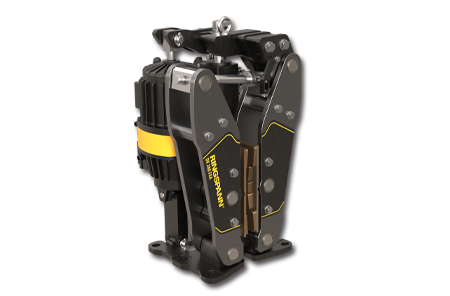
Electrohydraulic Thruster Brakes
- Robust self centering unit, that is easy to adjust
- Encapsulated automatic wear compensation unit
- Maintains parallel pad air gap when brake is released
- Very high braking force in a lightweight design
- Brake peak heights in accordance with the market standard: 160 mm, 230 mm, 280 mm and 370 mm
Electrohydraulic Thrusters for Hoists
Electrohydraulic Thrusters with gear pump
- For critical applications like main hoists and trolleys
- Pressure generation via gear pump
- Lifting forces up to 8 kN
- Ultra fast setting times (< 80 ms)
- 100% analogue layout – no circuit board required
- Proven 3-phase connection
- Very low power consumption due to unpressurised circulation, while brake is open
- Easy maintenance - wearing parts, such as solenoid coils, can be replaced while the thruster is installed in the brake
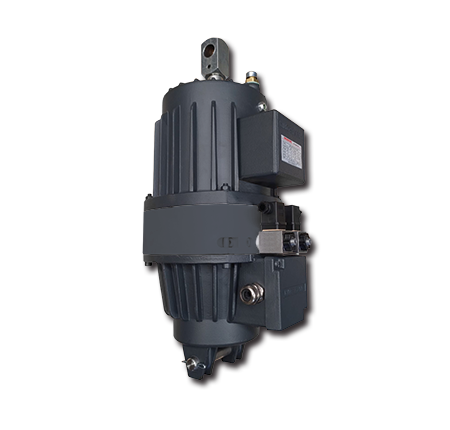
Electrohydraulic Thrusters with impeller pump
- Proven design with an impeller pump for pressure generation
- Simple and robust - easy to maintain design
- Lifting forces up to 4,5 kN
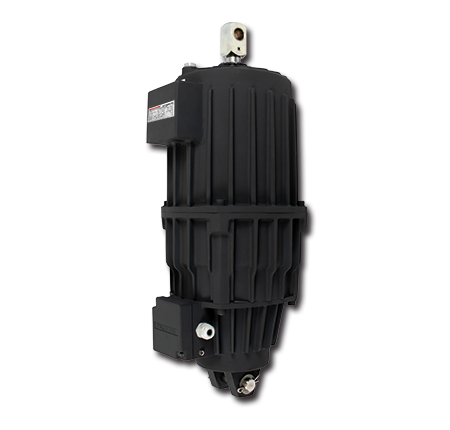
Emergency Brake Calipers and Hydraulic Power Units for Hoists
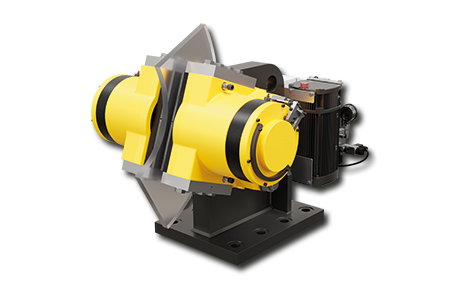
Hydraulic Emergency Brake Calipers
- Available as a fixed caliper version or as a floating caliper version to reduce weight and save space
- Hydraulic chamber mounted above the spring assembly allows for easy and safe brake seal replacement
- Optionally available as a ready-to-install solution with one or two brakes mounted on a pedestal, including hydraulic power unit, terminal box and hydraulic hoses or pipework
Hydraulic Power Units
- Modular setup allows a wide range of functions in one device
- Large range of options such as controlled braking, brake force adaptation or flank change elimination
- Optional accumulator for faster
- Optional accumulator for faster brake opening times, or ease of hand release
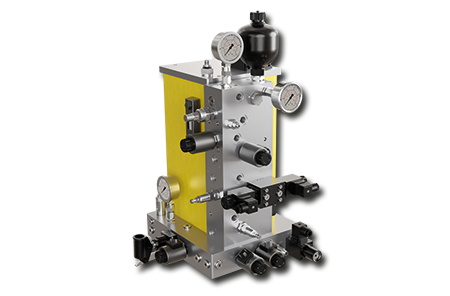
Storm Brakes for Gantry Drives
Rail Clamps and Rail Brakes
- Very high braking force with compact dimensions
- Easy and safe brake seal replacement with top mounted hydraulic chamber
- Suitable for all common rail profiles
- Inductive or mechanical sensors for “Brake open” and “Brake pad wear”
- Corrosion resistant coating up to C5-M (CX)
- Maximum holding force for rail clamp: 500 kN
- Maximum holding force for rail brake: 300 kN
- Rail clamp lateral float up to +/- 30 mm
- Rail clamp vertical float up to +/- 5 mm
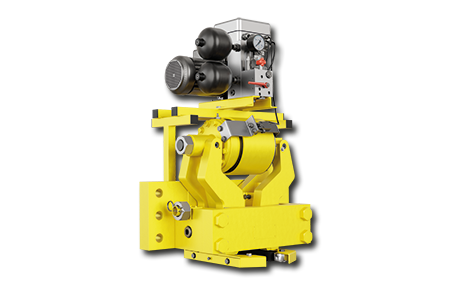
Service brakes for Gantry Drives
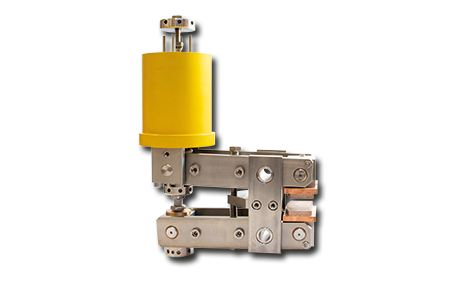
Electromagnetic Brake DH 034 FEM
- Simple and robust brake design
- Stainless steel levers for highest corrosion protection
- Suitable for dynamic and static applications
- Easy to install and maintain
Electrohydraulic Disc Brakes and Drum Brakes
- Drum brakes available in metric design according to DIN standard 15435 or with imperial dimensions according to AISE standard
- Robust and simple design
- Self-lubricating bushings
- Stainless steel pins and spindles
- Automatic wear compensation
- Organic or sintered linings for disc brakes
- Organic linings for drum brakes
- Optional self centering unit
- Optional throttle valve on the thruster for delayed brake setting
Solutions for extending the service life of hoist gearboxes
Braking systems for port cranes
Over the years, the size of container vessels have constantly been growing. This development has led to a growth of container cranes as well. Besides the increase in total height and boom outreach, the hoisting speed and maximum load under the spreader has grown, too. The result is an increase of peak torques in the bearings and the crane’s steel structure, when doing a category 0-emergency stop. | RINGSPANN has developed a complete range of braking solutions, that all follow one goal: To minimize the impact of peak torques and backlash to extend the lifetime of the gearbox. |
Flank Change EliminationA flank change in the gearbox occurs when the individual gears in the gearbox briefly lose contact with each other due to strong braking (e.g. during an emergency stop) and results in a damaging shock load. To eliminate a flank change, it is important to brake first on the transmission side, which is on the opposite side of the driving force. When lifting, these are the emergency brakes. When lowering, these are the service brakes. |
Adaptive braking on main hoistFor peak torque reduction, the braking force of the emergency brakes is adapted to match with the lifting situation: The required braking torque for a lifting or lowering process with an empty spreader is lower than the required braking torque for a lifting or lowering process with maximum load. During a lifting or lowering process with an empty spreader, a brake configuration is activated that provides sufficient but not excessive braking force; during a lifting or lowering process with a full load, all emergency brakes close immediately. In both cases, the hoist is safely brought to a standstill. |
Adaptive braking on boom hoistFor peak torque reduction during an emergency stop of the boom, the emergency brake caliper is able to brake with two different braking forces. This is achieved by the pre-selection of two different valve configurations on the hydraulic power unit. The first configuration allows immediate braking, the second configuration allows a 2-Step Braking with a reduced initial braking force which is increased over time. |
Detection of overspeed and gearbox failureWith the RINGSPANN Speed Monitoring Module SMM, we provide a PLC-based control unit which monitors the hoisting speed with the help of a combination of incremental absolute encoders which detect various conditions including gearbox failures, reversal rotation, and excessive speed. |
Solution: Flank Change Elimination
A common issue, that occurs during a category 0-emergency stop on a main hoist drive is the flank change in the gearbox. To avoid this unwanted effect, it is necessary to apply the brakes on the drive side, which are opposite to the driving force: |
|
To avoid a flank change, it must be ensured that both brake types - the emergency brake calipers on the rope drum and the electrohydraulic thruster brakes (service brakes) on the motor output shaft - always set in the correct order: |
|
Explanation of the flow chart
The RINGSPANN BCS for the elimination of flank changes consists of two key elements: An electrohydraulic thruster, which closes with two preset closing times, and a control unit, which pre-selects the respective closing time.
The system itself is a stand-alone solution in which the crane control system only needs to provide one single information: Is the crane in a lifting or lowering sequence? The solution is easy to integrate for both new cranes and retrofits to increase the life of the gearbox.
Solution: Adaptive braking on main hoist
When selecting a brake for a hoist, the maximum lifting speed in conjunction with the maximum lifting load is usually taken as a basis. Under operating conditions where the maximum lifting load and the maximum lifting speed both apply, the braking force of all brakes provides sufficient counterforce to stop the hoist in an emergency. | For example, if a crane is operated at 50% of its maximum speed and 50% of its maximum payload, the braking force of all the hoist’s brakes is too high. This results in very high peak torques in the gearbox, heavy impacts on the crane’s steel structure and high loads on all load-bearing bearings. |
The solution consists of three main components
|
Application
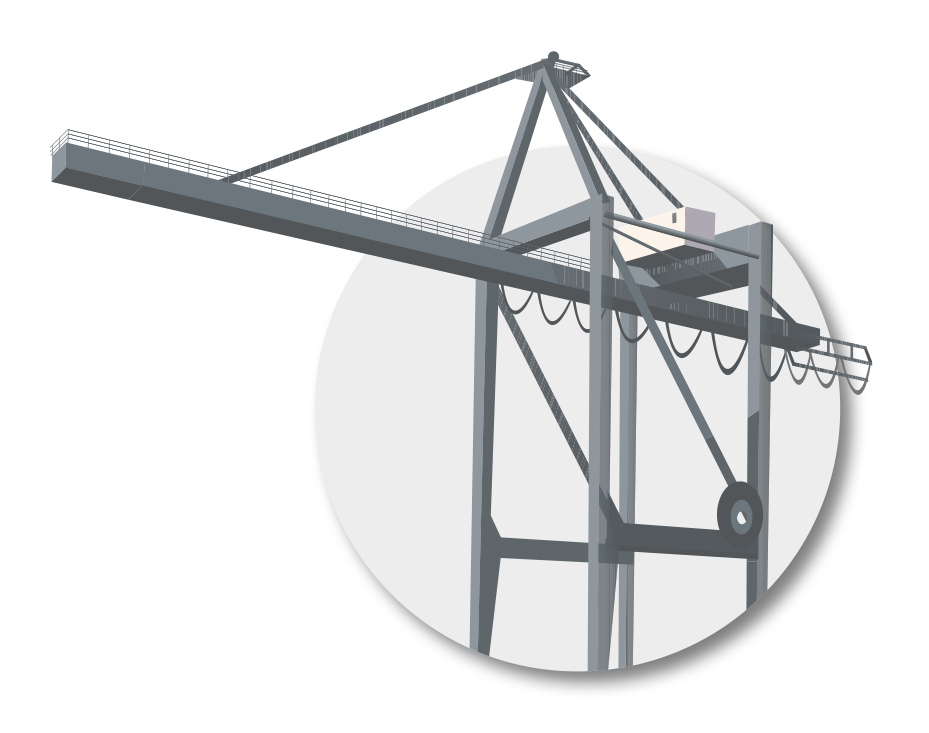
RINGSPANN Brake Control System BCS
Load case 1, 2 or 3
Explanation of the flow chart
The RINGSPANN BCS is simple and easy to integrate. A RINGSPANN control unit receives information from the Crane Management System about the status of the crane. Several load cases can be differentiated. For example, one possible load case can be travelling with an empty spreader at full speed. The control unit uses this information to set a predefined valve configuration on the RINGSPANN hydraulic power unit. For the aforementioned empty spreader travel, a brake configuration is activated that provides sufficient, but not excessive, braking force to bring the hoist safely to a standstill. The other brakes are automatically activated after a short delay and the full braking force is applied so that the crane is secured at a standstill. If required, this solution can be extended to include any number of brakes and load cases.
Solution: Adaptive braking on boom hoist
When container cranes are not in operation, the water-side boom is raised and brought into a vertical rest position. The reasons for this are, for example, to increase traffic safety (collision avoidance with approaching or departing ships) or to protect against the weather. | When the crane is prepared for operation, the boom is lowered. The load torque increases the closer the boom gets to the horizontal working position. The maximum braking force of the boom brakes is selected so that the boom can also be stopped and held close to the horizontal working position. |
If an unintentional emergency stop occurs when the boom is being raised or lowered, all brakes are applied with maximum force. This is problematic if the boom is close to the vertical rest position and damaging torque peaks occur on the gearbox, bearings and steel structure. | The adaptive braking to reduce the torque peaks during an emergency stop during the boom lift can counteract premature wear of the bearing, gearbox and steel structure. This is achieved by adjusting the braking force. Depending on the boom position, different valve positions are preselected on the hydraulic power unit of the emergency stop brakes. This reduces the braking force at the start of a braking manoeuvre at higher boom positions. |
Application
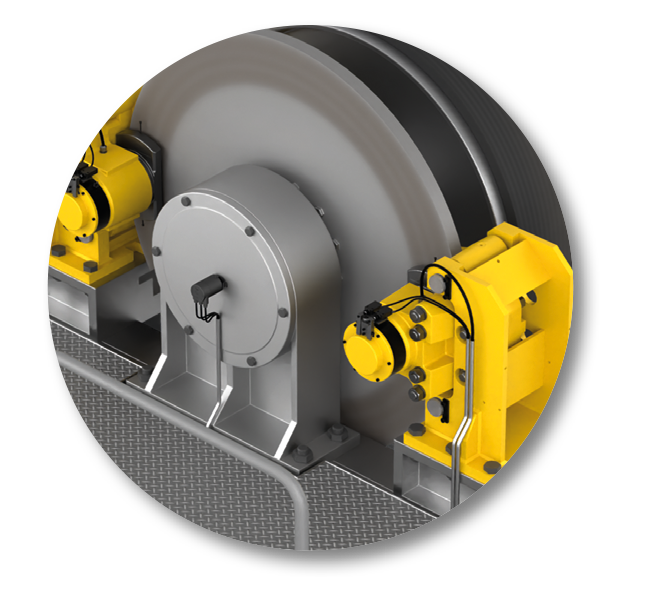
RINGSPANN Brake Control System BCS
Position of the boom
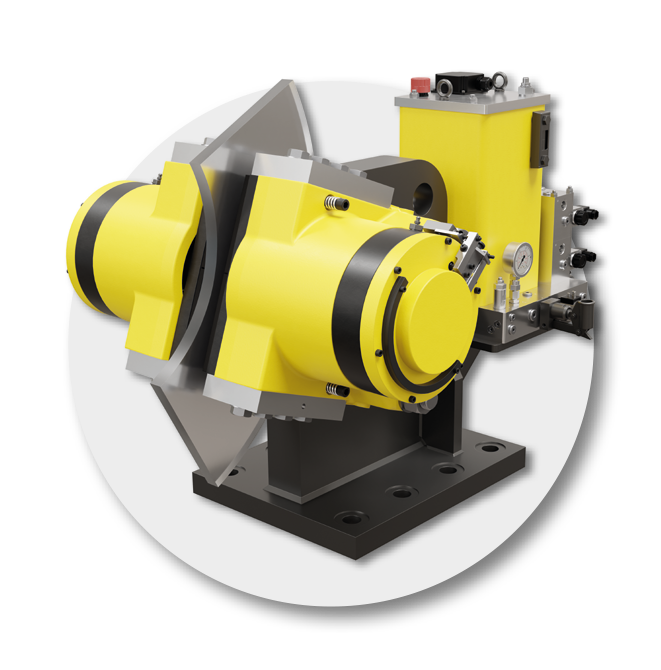
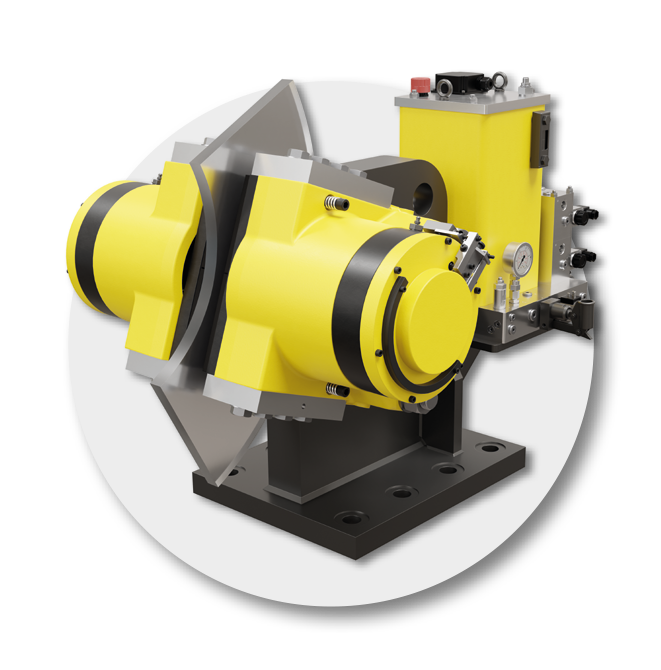
Explanation of the flow chart
The system consists of four components:- An absolute encoder, that is attached to the bearing of the cable drum and provides information on the position of the boom via the crane management system
- A control unit that processes the signal from the encoder and switches various valve states in the hydraulic power unit of the boom emergency holding brakes on this basis
- A hydraulic power unit that, through the combination of special detent valves, enables immediate braking as well as braking with reduced starting braking force that increases over a short period of time
- One or more emergency stop brakes that, in conjunction with the hydraulic power unit and the control unit, can initiate a braking process with different braking forces
Solution: Detection of overspeed and gearbox failure
Malfunctions can occur when hoists are in use. Therefore, it is advisable to equip the hoist with a suitable monitoring unit to ensure safe operation. RINGSPANN offers the Speed Monitoring Module SMM for this purpose, which reports potentially dangerous situations at an early stage so that countermeasures such as an emergency stop can be initiated quickly. |
Application
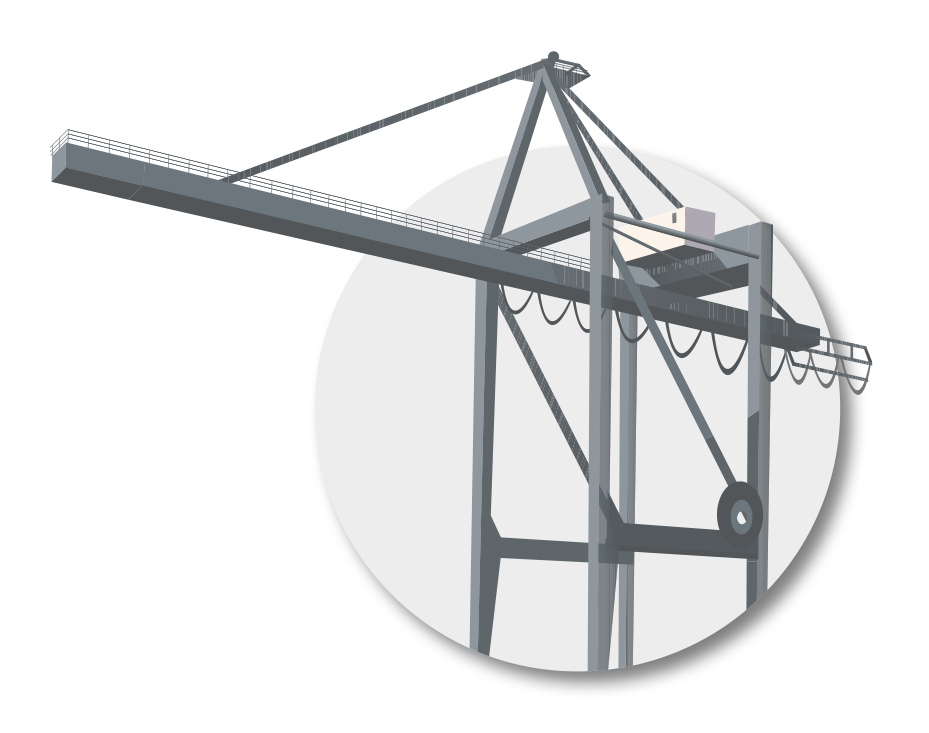
RINGSPANN Speed Monitoring Module SMM
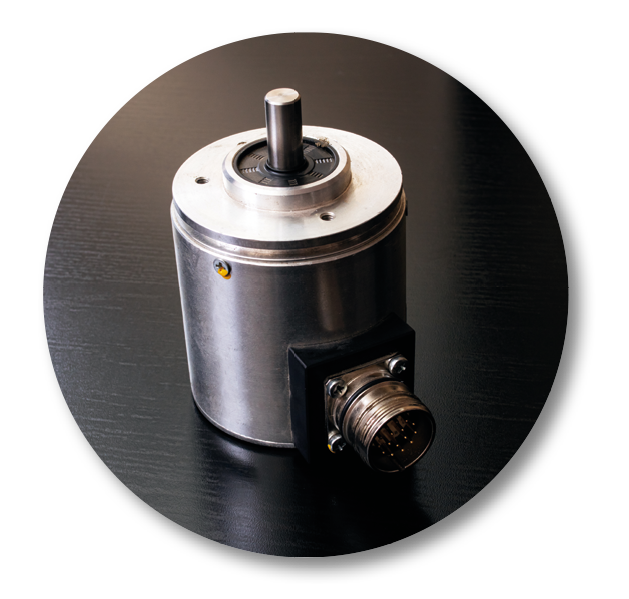
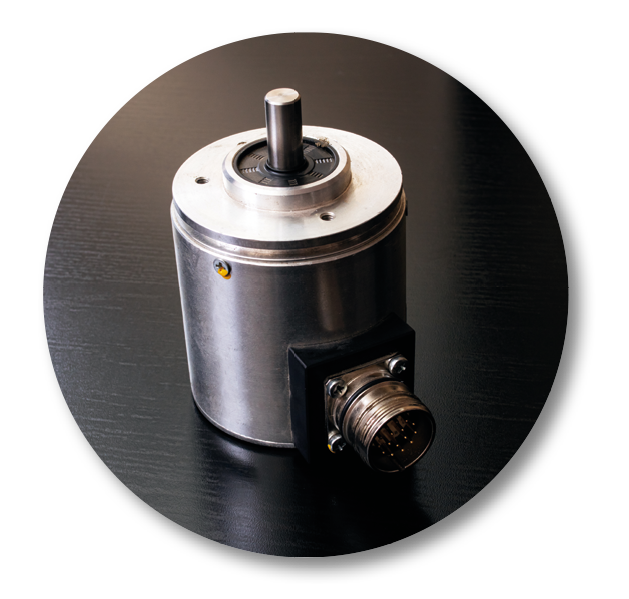
Explanation of the flow chart
The RINGSPANN Speed Monitoring Module SMM continuously monitors the signals from one incremental encoder at the gearbox input and one at the gearbox output. If preset limit values are exceeded (e.g. a limit speed during lowering), an error message is issued and sent to the crane management system. Alternatively, the SMM can also be combined with a BCS brake control system so that an emergency stop is executed immediately if a limit value is exceeded.